Introduction:In this case, we will discuss the successful implementation of a high-speed intelligent paper cup-making machine for a client in Turkey. The client, a leading paper cup manufacturing company in Turkey, was facing several challenges in their production process. They sought to enhance their productivity, reduce operational costs, and improve the overall quality of their paper cups
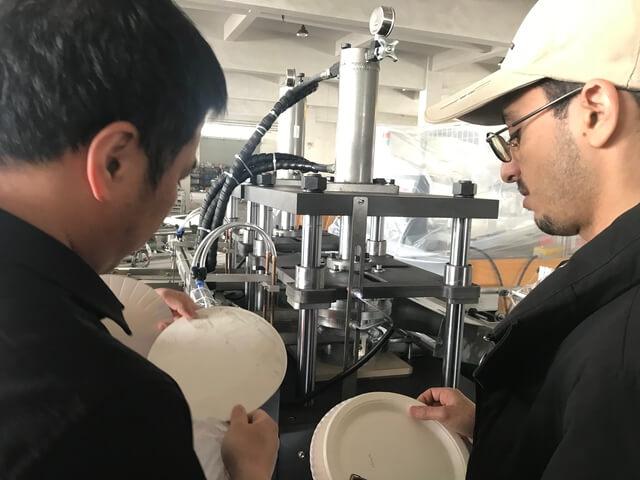
Client Challenges:
1. Low Production Efficiency: The client's existing paper cup-making machines were outdated and had a low production capacity. This resulted in longer lead times and limited their ability to meet customer demands.
2. High Operational Costs: The manual labor involved in the production process led to high operational costs. The client wanted to explore automation options that could reduce their dependency on labor and increase cost-efficiency.
3. Quality Control Issues: The client faced intermittent quality control issues, resulting in a higher rate of defective products. This affected their reputation and customer satisfaction.Solution:After evaluating their requirements, our company recommended the installation of a high-speed intelligent paper cup-making machine. This advanced machine utilized cutting-edge technology to address the client's challenges effectively.
Features of the Machine:
1. High-Speed Production: The machine had an impressive production capacity of up to 150 cups per minute, significantly increasing the client's production efficiency.
2. Automation and Precision: The intelligent features of the machine ensured precise cup forming, cutting, and sealing, eliminating human errors and enhancing product quality.
3. Energy Efficiency: The machine incorporated energy-saving mechanisms, reducing the client's operational costs by optimizing power consumption.
4. Real-Time Monitoring: The machine offered real-time monitoring and diagnostic capabilities, allowing the client to track production metrics, identify potential issues, and take corrective actions promptly.Implementation Process:The
implementation process involved the following steps:
1. Machine Customization: Our company worked closely with the client to understand their specific requirements and customize the machine accordingly.
2. Installation and Training: Our technical team installed and commissioned the machine at the client's manufacturing facility. They also provided comprehensive training to the client's staff on operating and maintaining the machine effectively.
3. Testing and Fine-Tuning: We conducted rigorous testing to ensure the machine performed optimally and met the desired production standards. Any necessary adjustments or fine-tuning were made during this phase.
4. Post-Installation Support: Our company provided ongoing technical support and maintenance services to the client, ensuring the smooth operation of the machine.Results and Benefits:The implementation of the high-speed
intelligent paper cup-making machine yielded significant benefits for the client:
1. Increased Production Capacity: The machine's high-speed capabilities allowed the client to meet growing customer demands while reducing lead times.
2. Cost Savings: Automation reduced labor costs, resulting in improved cost efficiency for the client
3. Enhanced Product Quality: The advanced features of the machine ensured consistent and precise cup production, minimizing defects and improving overall product quality.
4. Improved Customer Satisfaction: With faster delivery times and superior product quality, the client experienced higher customer satisfaction levels and an improved reputation in the market.Conclusion:The successful implementation of the high-speed intelligent paper cup-making machine brought about a transformation in our client's manufacturing process. By addressing their challenges and providing them with a state-of-the-art solution, we helped them achieve higher productivity, cost savings, and enhanced product quality. This case demonstrates the positive impact that advanced technology can have on a company's operations and competitiveness in the market.